A Systematic Approach to Enhance Value, Lower Cost and Maintain Function
One of the most misunderstood processes in the building industry, from construction to engineering to product manufacturing, is value engineering. Value engineering is “a systematic approach that seeks to enhance value by eliminating unnecessary cost while maintaining function.”
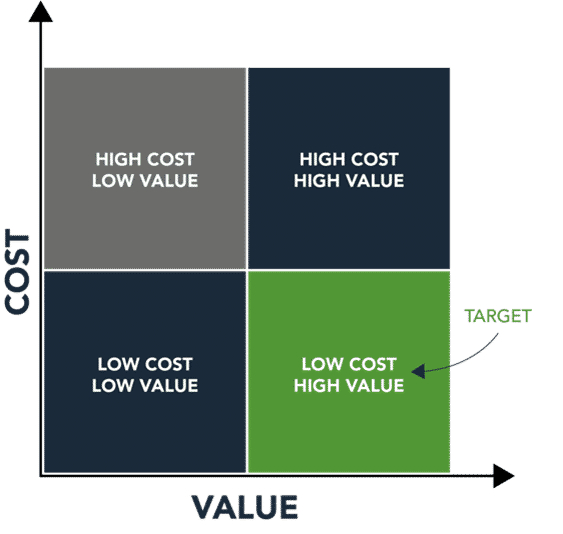
For most, the term value means low cost or budget-cutting, thereby reducing quality when defining the value is different for everyone and doesn’t always mean cutting costs.
The main objective of value engineering is to achieve the best value —maintenance, durability, long-term viability, aesthetics, and more — not just cutting costs.
Value engineering is not a new trendy term. During World War II, the country experienced material, parts, and a skilled labor shortage. At the time, General Electric engineers set out to source alternative and acceptable materials and components to continue manufacturing without compromising the integrity of the products.
Lawrence Miles, touted as the father of value engineering, lead the charge at General Electric, and today his value engineering techniques are used throughout the world. The Lawrence D. Miles Value Foundation advances the value engineering methodology with educational programs, international conferences and forums, new applications, and a research library.
Today, engineering and construction firms and product manufacturers employ a value engineering process. Each follows its standards and phases to achieve the end goal: to increase value at a low cost while maintaining optimal functionality. Value engineering is required for almost all government and military projects as well.
The process of value engineering is best when performed in the design phase. The subject matter expert involved in the project can incorporate the best options to improve the value from both the project and product perspective.
Value Engineering and Cable Railing Specification
There are many components to consider when specifying cable railing — number of posts, stainless steel cable, fittings, hardware — and installation, whether it’s new construction or a retrofit. Maximizing post placement and the frame integrity can significantly change the fittings and hardware used on the project and affect the bottom-line cost.
Using a rooftop deck as an example, install a double post in each corner opposite the building (or other structure) and a terminating post offset about two- to three-inches from the building for easy tensioning. This combination offers the most support and a smaller, concealed tensioner fitting option using our concealed Invisiware® receivers for a clean and seamless appearance. It also enables the cable to run continuously through the length of the run and through all posts, in most cases, — even around corners — without stopping and starting at each post.
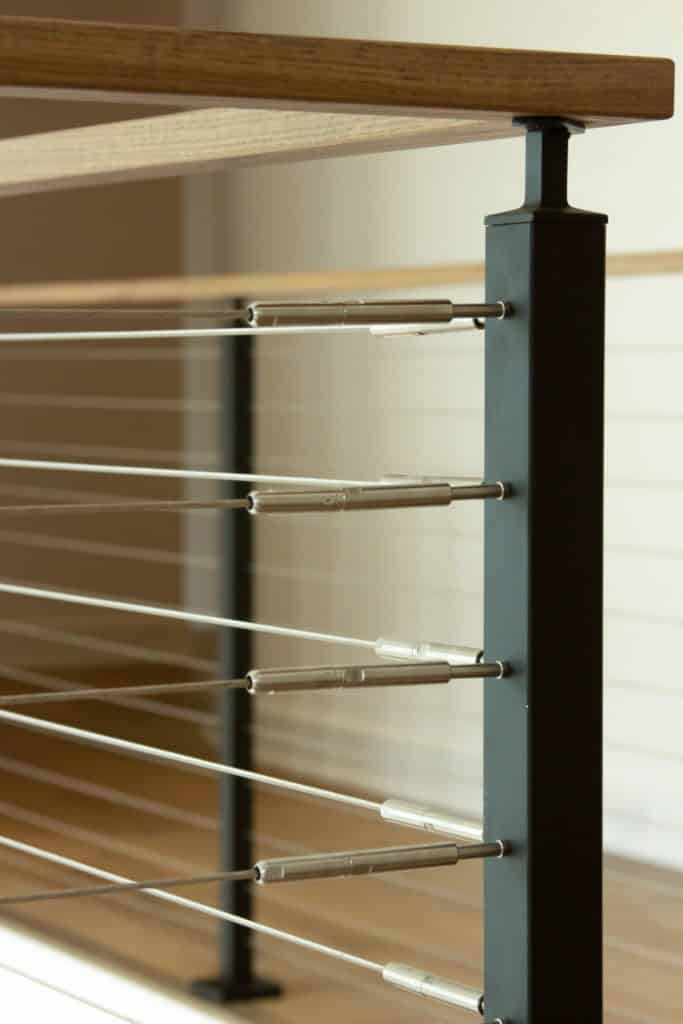
In contrast, if using a single corner post option, the cable will typically terminate at each corner. In this scenario, the cable stops and starts at each post increasing the number of fittings required. Stopping and starting more often not only drives up cost, but it also changes the aesthetics and most importantly the integrity of the frame. That significantly increases the amount of tension on that single post, which jeopardizes the strength of the frame and its ability to maintain properly tensioned cables adding to the overall cost of the project.
At first glance, double corner posts may not seem aesthetically appealing until you compare it to the added exposed fittings required for a single termination post. See for yourself how you can achieve the high-end look with an unobstructed view using a double corner post setup for a cost-effective, seamless, and modern finish.
Value Engineering is not a one-size-fits-all process that simply cuts costs to save the budget. A holistic view of the project and the specifications are necessary to offer a beneficial solution that meets the customer’s goals without compromising functionality.
Recent Comments