Ultra-tec stainless steel cable railing products are an excellent choice for a variety of commercial designs, offering unobstructed views and a spacious appearance. The most common use of cable railings in designs today are horizontally run cable railing system for interior and exterior applications.
The use of cable railings for commercial projects offer architects and designers flexibility, versatility, and a modern approach to any design. Cable railings also allow a creative and easy to install alternative for fabricators and installers. In addition to design and creativity, there are key design considerations for a successful cable railing system installation.
Stainless-Steel Cable Railing Strength
Cable, also referred to as wire rope or aircraft cable, is very strong in tensile strength and is designed to be flexible. The degree of flexibility varies depending on the cable’s diameter and construction (1×19, 7×7, 7×19, etc.), the tradeoff for flexibility is strength, and the opposite is also true.
For commercial projects or anywhere there is heavy pedestrian traffic, we recommend a 3/16-inch diameter cable (316-grade stainless steel). It is most commonly used and is durable, low-maintenance, and is attractive. For a variable aesthetic option, other diameters are available from 1/8-, 1/4-, 5/16-, and 3/8-inches.
Stainless-Steel Cable Railing Flexibility
Cable flexibility is an important consideration when designing a cable railing application. The International Residential Code (IRC) and International Building Code (IBC) require that a 4-inch sphere shall not pass through any portion of the installed railing. Because of this code requirement, the use of the most rigid of cable construction possible is ideal. Having the rigidity to prevent deflection of a horizontal run cable subjected to a vertical load is partly mitigated by the cable’s lack of flexibility.
The IBC requires cable designs to withstand a single concentrated load of 200 pounds applied in any direction at any point along the top. Also, attachment devices and supporting structures — handrails and guards — transfer the load to structural elements of the building.
Other factors include the tension — to at least 225 pounds — of the cable, the span between supporting intermediate members, the cable’s diameter, the vertical spacing of the cables on center, and temperature at the time of installation. Temperature fluctuations can cause variations in cable tension due to differing thermal expansion of the railing frame and the cable. Depending on geographic locations, cable railings installed outdoors may experience large swings in temperatures; hot summer days to the cold winter nights may be a 140-degree difference.
The use of a stainless-steel railing frame virtually eliminates temperature-induced tension changes because it contracts and expands at the same rate as the stainless-steel cable.
Alternative materials like carbon steel, aluminum, and wood each expand differently than stainless and railing frames made from these materials and will exhibit varying cable tension with changes in temperature.
Post Spacing for Cable Railing
Intermediate posts or braces support the cable as it passes through the railing frame’s posts. An intermediate post is a structural post that runs from the top rail to the mounting surface, and a brace is a lighter weight material, supporting the cable and placed between posts.
While cable can run quite long distances (as much as 60-feet or more) between end posts, it will need support at intervals — intermediate posts or braces — to avoid cable deflection in excess permitted by building codes.
It is recommended to space posts or braces at a maximum of 48-inches with center cables 3-1/8-inches apart.
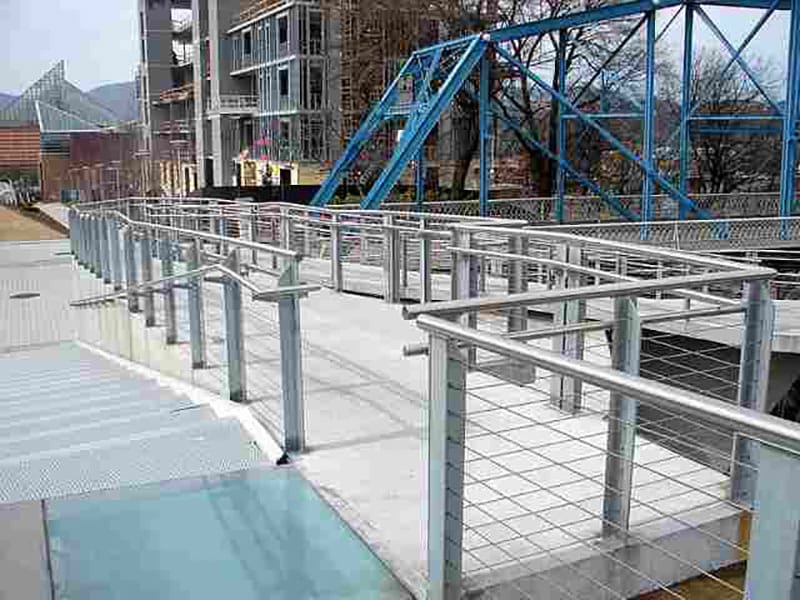
Stainless-Steel Cable Railing Tension and Top Rail
Mounting and tensioning hardware is attached to end posts and work together to minimize the deflection. Posts must not deflect perceptively as the cables are tensioned to a minimum of 225 pounds at heights of 36- to 42-inches. It is crucial to minimize end post deflection, and potential bending, as an incredible amount of force is placed on the end post with ten or more lines.
A sturdy top rail is required to support the tensioning end posts and prevent bending under the strain of the tensioned cables. The most commonly used top rail for commercial use is stainless steel due to its resistance to corrosion and low maintenance.
Designing with Stainless Steel Vertical Railings
Vertical cable railings — cables run from the top rail to the bottom rail — are becoming increasingly popular to differentiate a project for either interior or exterior use. The building code requirements apply to vertical cable railings; however, the installation of vertical railings differ.
Framing material — pipe, or structural square or rectangular tube framing (stainless steel for exterior use) — with a minimum wall thickness of ¼-inch is ideal. Cable braces are appropriate for replacing every eight cables to keep the top and bottom rails from bending when the cables are tensioned.
In this example, we recommend using the Invisiware® Threaded Stud on one end of the cable and screwed into a drilled and tapped hole in the underside of the top rail. An Invisiware® Receiver inserted into a hole drilled through the bottom rail. A threaded stud on the other end of the cable, tensioned by turning the receiver with an Allen wrench, completes the run.
Stainless steel cable railings and fittings offer a beautiful, low maintenance option to enhance interior and exterior designs. Ultra-tec products also contribute to LEED® credits benefiting architects, designers, and building owners to achieve required building certifications.
To learn more, contact us.